- BOAT OF THE YEAR
- Newsletters
- Sailboat Reviews
- Boating Safety
- Sailing Totem
- Charter Resources
- Destinations
- Galley Recipes
- Living Aboard
- Sails and Rigging
- Maintenance
- Best Marine Electronics & Technology
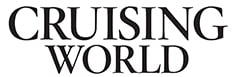
- Uncategorized

Prop Shaft Alignment
- By Perry Munson
- Updated: June 8, 2011

Regarding John Gross’ question about how a shaft can be aligned with so many things being so wobbly: A shaft can’t be aligned if it’s wobbling around. You must first take the wobble out of it, then align the coupling flange on the transmission to the flange on the forward end of the shaft. Here’s one series of tricks that actually works if your boat is out of the water.
1. Loosen the hose clamps and remove the rubber boot from the front end of the shaft log.
2. Slide it and the packing gland ahead on the shaft.
3. Disconnect the two coupling halves connecting the shaft to the transmission by removing the four bolts holding them together. Slide the shaft back a bit, perhaps 1/2 inch.
4. Slip four pieces of carefully milled hardwood or square steel rod back a couple inches into the shaft log around the shaft, one each on the top and the bottom and one each on the sides. This centers the shaft in the shaft log and gets rid of the wiggle, assuming your cutless bearing was recently replaced. For instance, if the inner diameter of the shaft log is 1.5 inches and you have a 1.0 inch shaft, the square rods (whatever they’re made of) will have to measure 1/4 inch by 1/4 inch by whatever length is convenient. Now the shaft is stabilized.
5. Carefully wrap duct tape around the exposed rods so they stay in position on the shaft and keep it centered.
6. Slide the shaft forward (the rods will have to slip back and forth on the shaft or in and out of the shaft log a bit) until the shaft flange butts up against the transmission flange loosely.
7. Note the variations in the gap between the two halves. Slide the shaft back again 1/2 inch.
8. Using the adjustment nuts on your engine mounts, move the engine so it’ll take up the slack. Like this: If the coupling halves clicked together at the bottom but had a small gap at the top, the front of your engine probably has to go up some. This can also involve some port-starboard adjustment if there’s a sideways gap. Do whatever it takes. Any reputable engine mount offers the ability to make vertical and lateral adjustments.
9. Slide the shaft forward again so the two flanges click together loosely.
10. See how you did in adjusting the engine’s position so that the two flanges fit together snugly all the way around.
11. Check the gap using a feeler gauge. If the gap is more than 0.004 inch on any side, adjust the gap again.
12. Keep repeating Steps 6 through 10 until you get it right. The less gap the better. Ideally, the coupling halves should slide together easily and butt up to each other with no gap. This process of repetitive adjustments may take a few hours. If you get burned out, go home and come back. Having your most mechanically astute friend helping you will relieve the stress a lot.
13. When everything looks good, tighten down your engine-mount nuts, do a final check, then bolt the two flanges back together. Tighten all nuts a little, then go around again and do the final tightening. Check the set bolt that holds the coupler onto the shaft for tightness. Make sure it has a keeper wire around the coupling and through the hole in the square bolt head.
14. Finally, remove the rods centering the shaft in the shaft long, slide the boot and packing gland back so the boot is back to where it was, and cinch down both hose clamps. If you put the transmission in neutral and slowly rotate the prop shaft by turning the coupler around, you should see essentially little or no wiggle in the packing gland and the flexible boot behind it. If you start your engine and let it run at idle, everything will be jiggling and wiggling some as it’s supposed to. That’s why engines have a flexible boot between the packing gland and the shaft log and four flexible mounts. As the engine approaches operating speed, around 2500 to 3000 rpm, under load on the water, the jiggle should go away, and there should be no gross movements, only an engine and shaft humming away in a steady state. The transmission and cutlass bearing should now be able to enjoy extended lifetimes. If you plan to go cruising very far from home, this is a skill you should have. Doing an alignment requires great care and patience.
Perry Munson Baltika , Nor’Sea 27 Grosse Pointe, MI
- More Uncategorized

Schooner Nina Missing
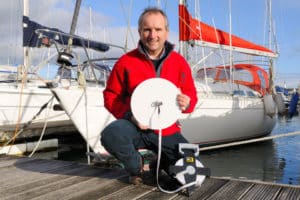
Editor’s Log: Pitch In for the Plankton
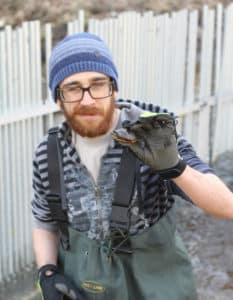
West Marine Announces $40,000 Marine Conservation Grants for 2013
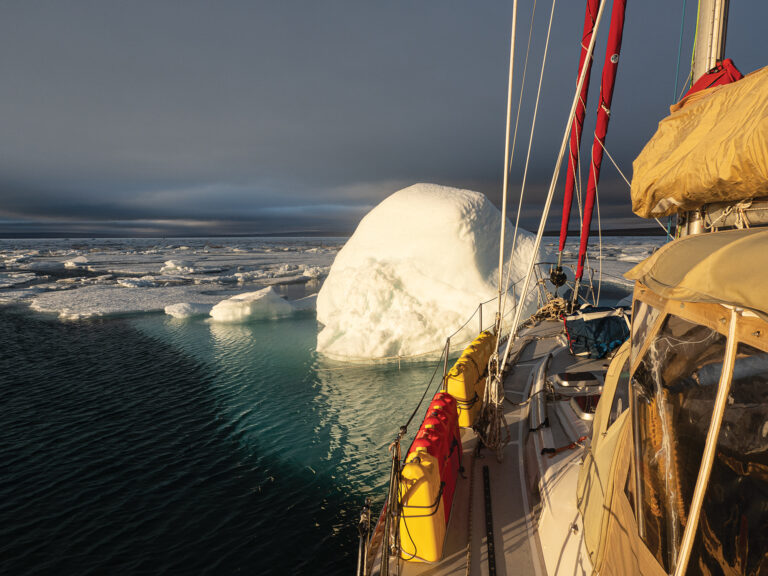
Cruising the Northwest Passage

Balance 442 “Lasai” Set to Debut

A Legendary Sail

10 Best Sailing Movies of All Time
- Digital Edition
- Customer Service
- Privacy Policy
- Email Newsletters
- Cruising World
- Sailing World
- Salt Water Sportsman
- Sport Fishing
- Wakeboarding
- MarketPlace
- Digital Archives
- Order A Copy
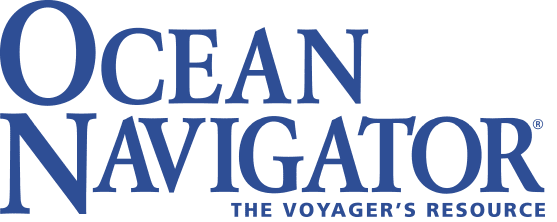
Prop shaft alignment
Nearly all marine engines are designed to be adjustable, to a point, relative to the propeller shaft by using adjustment or jacking nuts on their motor mounts. The adjustment should be thought of as no more than fine-tuning, the maximum range of vertical travel being limited to no more than an inch or two at the most, which is substantial when one considers that alignment is typically measured to just a few one-thousandths of an inch. Thus, the responsibility rests with the naval architect and boatbuilder to ensure that the design and execution of the engine installation guarantees near-perfect alignment with the shaft before the motor mounts are adjusted.
The other alignment There is another side to the alignment story; it involves the support and position of the propeller shaft relative to its bearings, the shaft log (the tube through which the shaft passes) and the engine. While engine alignment is, or is expected to be, well understood by most marine industry professionals, shaft alignment is, on the other hand, far more esoteric and well understood by far fewer in the industry. In my experience, precious few truly understand its importance and the consequences of misalignment, and fewer still understand the techniques and processes involved in making adjustments and corrections.
Contrary to popular belief, shaft misalignment rarely leads to vibration, as the bow or offset induced in a shaft by misaligned bearings is constant. Improper shaft alignment can lead to excessive shaft drag and a resultant increase in fuel consumption, as well as accelerated bearing and shaft wear.
A few years ago, I inspected a vessel while it was hauled out. When I came to the propeller, I made an unsuccessful attempt to rotate it in order to gauge the condition of the bearings and alignment. Regardless of how hard I tried, I was unable to rotate either shaft on this twin-screw 60-foot vessel. This is a clear indication of either severe shaft misalignment (as opposed to engine misalignment, which rarely imparts this sort of resistance) or, less commonly, swollen shaft bearings. While final alignment of an engine to its shaft should only be carried out once a vessel has been afloat for 24 hours, even when hauled out the shaft should turn without undue effort once adhesion between it and its bearings is broken.
How shaft bearings work In virtually all cases, propeller shafts are supported by one — and for longer shafts, sometimes as many as four — bearings, often referred to by their trade name, “cutless bearings.” Shaft bearings are pipe-like components, the outer shell of which is typically made of brass, or sometimes a fiberglass-like material (the latter is designed to be used on steel and aluminum vessels to avoid the corrosion potential caused by copper alloys), with an inner liner of grooved or fluted rubber. It comes as a surprise to many users that the sole source of lubrication and cooling is seawater; if water flow to the bearing is insufficient, or if it’s interrupted by marine growth or a line, net or other debris on the shaft, or if the shaft log water injection system is clogged, rapid bearing wear can ensue.
Shaft bearings may be found in and supported by struts — I- or V-shaped metal supports attached to the vessel’s hull, through which the shaft passes — and/or embedded within the shaft log in the keel or hull. When the vessel is built, the builder must make a concerted effort to ensure that bearings are properly located to support the shaft, while ensuring that they are also aligned with the theoretical shaft’s centerline, a line that is perpendicular with and begins at the center of the transmission output coupling, traveling aft through the bearings. The line must also be centered in and parallel with the bearings. If the builder is successful in ensuring this alignment, barring groundings or other damage, it should remain correct throughout the life of the vessel. While small adjustments may be made to the relationship between the engine and shaft by adjusting the location of the former, the shaft’s relationship to and alignment with the bearings should remain constant.
Analysis and adjustment In practice, it’s not uncommon to encounter shafts and bearings that are misaligned, and the greater the number of bearings, the greater the likelihood of misalignment. While shaft-to-bearing alignment can be challenging, aligning a shaft to several bearings, as well as the general location of the engine, can be daunting. As such, it’s easy to see how this process can go awry while the vessel is being built.
Traditionally, during construction or repairs, the process begins with a length of small-diameter yet stout string or wire, which is adhered to the center of the transmission output coupling. It is led aft through the shaft log toward the rudder, where it is anchored typically to a weighted object like a jack stand. Using this string or wire as a reference point, bearings (and, if present, struts) are positioned. When properly aligned, the bearings must remain centered on and parallel with the string or wire.
While this traditional approach is still used, more modern tools are now routinely employed; these include lasers and optical sights. Using a laser or sighting tool, an installer can position one or more bearings along the sight line with great accuracy. While this aspect of shaft alignment is critical, it’s the easy part. Setting the bearings in place permanently can be more challenging.
Initially, the strut or bearing is “dry fit.” That is, it’s positioned roughly to determine what needs to be done to align it with the shaft. The process typically involves a technique known as “casting.” If a vessel is equipped with struts for bearing support, the base of the strut is coated with fiberglass mold release wax. It is then set into a mixture of thickened reinforced epoxy and positioned so that it remains centered on and parallel with the string, laser or optical sight or shaft line. The strut is “hung” from support fasteners, and wedges are used to adjust its height and orientation to the shaft centerline. Once the position is set, the epoxy is allowed to cure, after which — thanks to the wax — the strut is easily removed. Wax is removed from the strut and the epoxy surface, and the strut is then set in bedding compound, ensuring a watertight seal with the hull. In some cases, the bearing centerline may be below that of the shaft. In this instance, depending on the degree of misalignment involved, a recess may have to be made in the hull to accept the strut’s base, the strut may require modification or a new strut may need to be manufactured altogether.
A similar process is employed for bearings that reside within a shaft log and strut. The bearing itself is waxed and set in epoxy, and wedges are used to position it so that it remains parallel with and centered on the shaft line until the epoxy cures. All bearings should be a light press fit in the shaft log or strut. Ultimately, bearings are retained using set screws; a minimum of two must be used, and they should be installed at 60 degrees to each side of the bottom centerline, or at the 4 o’clock and 8 o’clock positions (alternately, they may be installed at the 3 and 9 o’clock positions, but not above the horizontal shaft centerline). Set screws must be harder than and galvanically noble to the bearing shell; indentations (not holes), which the set screws engage, should be drilled into the bearing shell using a drill bit with a tip angle that matches that of the set screw. A thread-locking compound should be used on set screw threads.
Ultimately, once the shaft-to-bearing alignment is complete, even a long and large-diameter shaft should — with the benefit of nothing more than light lubrication from soapy water — rotate with relative ease using one hand.
Before entrusting your vessel to anyone for shaft alignment analysis or adjustment, carefully scrutinize their knowledge and experience on this all too important yet frequently misunderstood subject. Don’t lead; simply ask, “How do you ensure the shaft is properly aligned to the bearings?”
Steve D’Antonio is an ABYC-certified master technician and owns Steve D’Antonio Marine Consulting.
By Ocean Navigator
- If this is your first visit, be sure to check out the FAQ by clicking the link above. You may have to register before you can post: click the register link above to proceed. To start viewing messages, select the forum that you want to visit from the selection below.
Announcement
How to check and adjust propeller shaft alignment.
- Latest Activity
- Time All Time Today Last Week Last Month
- Show All Discussions only Photos only Videos only Links only Polls only Events only

- Join Date: Aug 2010
- Posts: 1568
- Location: Long Beach, CA
- Boat: 2015 Z3, 1999 2100i

- Join Date: Feb 2016
- Posts: 3217
- Location: Boise, ID
- Join Date: Oct 2018
- Location: Parker, TX
- Boat: Tige R23

- Join Date: Aug 2016

- Join Date: Feb 2022
- Location: Windber, PA
- Boat: '06 24V
- THE PRINCESS PASSPORT
- Email Newsletter
- Yacht Walkthroughs
- Destinations
- Electronics
- Best Marine Electronics & Technology
- Boating Safety
- Uncategorized
Shaft Alignment
- By Vincent Daniello
- Updated: September 15, 2009
ytgsep15yy525.jpg
Advances in hulls, engines, propellers, and even acoustic materials have all made boats stronger, faster, and quieter. Today we’ve come to expect luxury-car comfort aboard 100,000-pound yachts traveling 30 knots. But the shafts, struts, and bearings that tie engines to props have changed little since the mid-1800s when the screw propeller eclipsed the paddle wheel, and quirks in this drive train often cause vibrations. Fortunately, a few specialists are employing sophisticated methods to find and eliminate vibrations from shaft and strut technology that far predate the Model T.
“Everyone wants their boat to run like a Lexus. They don’t want to feel a thing,” says Fred Zucker, president of Seaworthy Services in Palm Beach Gardens, Florida( www.oceanalloys.com ). “Unfortunately, the human body is particularly sensitive to the frequencies of vibrations typically found on yachts.” Zucker has been building yachts and chasing vibrations for over 35 years, back when a mechanic’s experience, intuition, and the soles of his feet helped track down annoying, repetitive thumps.
“We learned from trial and error what makes a boat shake,” Zucker says. “We’d take boats apart, fix something, put them back together, and go on a sea trial, but often we’d still get fooled.” Today Zucker relies on years of acquired knowledge, but uses sensitive accelerometers connected to computers to analyze the sources of onboard vibrations. “When something is thumping, we want to know how many times a minute-the vibration’s frequency-and how hard-its amplitude,” Zucker says. By determining the frequency, Zucker can match it to the offending equipment. A bent propeller, for instance, will vibrate at some multiple of shaft speed, depending on how many blades are damaged, whereas a bent propeller shaft taper is subtly different.
“You’ll see an abnormal propeller signature,” Zucker says, “But you’ll also get a thumping vibration at the frequency that the propeller shaft is turning.” Problems originating from an engine itself will usually show up at one half of engine rpm since, on four-stroke diesels, each cylinder fires on every other rotation of the engine. Misfiring generators, too, will vibrate at half their rpm, and other pumps and equipment can be tracked down similarly.
Zucker warns, though, that while measuring vibrations is an exact science, interpreting the results is still largely an art. “This is complex machinery moving in a dynamic environment,” he says. “You’ve got to understand the construction of the boat you’re working on as you’re taking these readings.”
Zucker says one common misdiagnosis is mistaking an exhaust issue-producing a vibration frequency that is some multiple of the number of cylinders times engine rpm-for a propeller problem-which vibrates at the rate the shaft is turning times the number of propeller blades. The close frequencies often compound either issue. “A vibration may start out as an exhaust problem at lower speeds and then become a propeller problem at higher speeds. Somewhere in between, if those two frequencies overlap, they may cause a much larger vibration than either the exhaust or the propeller would independently.”
Finding the cause, or causes, of vibrations is only half the battle. While many specialists employ equipment and techniques similar to Zucker’s, Seaworthy Services actually does the work necessary to mitigate the shakes. “There are some very smart people doing [vibration analysis],” Zucker says. “But we sea trial the boats and see the computer diagnosis, and then we take the nuts and bolts apart and actually see the problem, and either prove or disprove what the computer is saying.” Zucker enjoys the instant gratification, and he also learns nuances from each repair that aid him in future, tricky diagnoses.
As mentioned, misaligned propeller shaft bearings are responsible for many vibration issues. Zucker says about half of the boats he works on for vibration mitigation have at least one misaligned or misplaced strut or shaft log. The shaft log is the tube that allows the shaft to penetrate the hull, with the stuffing box or shaft seal at one end, and typically a bronze and rubber shaft bearing within. Fortunately, resolving these alignment issues has gone high-tech, too.
“The first step, and the key to getting it right, is to make sure the yard blocks the boat just like it sits in the water,” Zucker says. The age-old method relied on strings or wires suspended tightly across the boat, with measurements taken from these wires to key points. Today technicians use laser equipment developed for land surveying, which shoots beams of light at precisionadjustable horizontal and vertical angles. “We use multiple laser systems and set up numerous targets before the boat is hauled,” Zucker says. “Then we make sure we hit those targets again as the boat is blocked.” The goal is to prevent misshaping or twisting the hull by supporting it exactly as the water does. Engines, too, are targeted, so they remain in the precise position they’ll take when the boat is relaunched.
With the boat sitting on land just as it floats, and with the propeller shaft removed, Zucker shoots a laser from the propeller’s normal position, up through each strut and the shaft log, off a mirror placed on the transmission’s shaft coupling that bounces it back toward the propeller. “Each laser is set up on four-plane micrometers,” Zucker says. “We can adjust them up and down, side to side, or tilt them, measurable in thousandths of an inch.” Inserts in each strut ensure the laser finds both the strut’s center and angular alignment to within thousandths of an inch, and a target on the forward-facing surface of the insert indicates how far off center the reflected laser beam is. “When that laser beam shoots up to a mirror on the transmission’s coupling and straight back into itself, we know we’re dead-on,” Zucker says.
Rather than moving each strut, Zucker looks for at least two points that are aligned within tolerances, and moves other components to match, reducing the job cost. Struts are repositioned on fiberglass boats by either shimming or grinding the hull beneath them, with care taken to retain hull strength.
As the shaft bearings are aligned, the engine is also brought into precise alignment with the shaft. “Even experienced yacht people think that if you get the two faces of the propeller shaft coupling exactly parallel, the engine is aligned, but you’ve got a huge amount of weight, seven or eight feet of shaft and a heavy coupling, hanging out there unsupported once it leaves that last bearing,” Zucker warns. “All too frequently we find that the front end of the engine is about a quarter- to a half-inch low. The back is a bit low, too, because the engine had been aligned to a drooping shaft.” Zucker’s technicians prevent this with the same laser system, raising or lowering each of the four corners of an engine until the transmission’s output shaft is exactly parallel to and centered with the propeller shaft. A laser reflected off the coupling verifies the angle, and shooting it into a precisely centered target ensures vertical and horizontal alignment.
Zucker has further streamlined his system with high-resolution cameras viewing the laser targets and broadcasting to monitors in the engineroom and at the laser. “Rather than having one guy outside the boat telling someone inside the boat which way to move the engine, one or two guys working entirely within the engineroom can align an engine very quickly,” Zucker says. “When we slide the shaft up, we check that the coupling surfaces are parallel with a feeler gauge, but we’re usually within one or two thousandths. You can’t machine a shaft and coupling with the kind of accuracy we’re getting.”
Even with everything precisely aligned, some boats still vibrate. “Sometimes struts themselves will move. It’s a resonant frequency response to the shaft spinning through the strut. If you go a little faster or a little slower, it usually goes away, but a minor nick in a propeller blade may excite that strut and cause a noticeable vibration,” Zucker explains. “Like a tuning fork, there will be some frequency that every single-leg strut will vibrate at. Hopefully it is not at cruise rpm.” To avoid this, yacht designers try to design struts with resonant frequencies outside the normal range of propeller shaft rpms, though they’re not always successful.
Zucker and other vibration experts tell of innumerable variations and dozens of oddball circumstances that cause hard-to-find vibrations. In the past, yacht owners often just accepted them as too expensive or troublesome to find. But thanks to technology, today every boat can ride like a Lexus.
- More: Systems
- More Uncategorized
BoatUS Launches Online Advocacy Tool
Dock danger, a dream fulfilled, 3 america’s cup hashtags to follow, power catamaran popularity rising, for sale: sunseeker predator 68, for sale: cl yachts clb 72, 10 yachts under $500,000 you can have today.
- Digital Edition
- Customer Service
- Privacy Policy
- Email Newsletters
- Cruising World
- Sailing World
- Salt Water Sportsman
- Sport Fishing
- Wakeboarding

- Forum Listing
- Marketplace
- Advanced Search
- About The Boat
- Gear & Maintenance
- SailNet is a forum community dedicated to Sailing enthusiasts. Come join the discussion about sailing, modifications, classifieds, troubleshooting, repairs, reviews, maintenance, and more!
Prop shaft alignment

- Add to quote
I need to align my prop shaft. I know there are ways to check the alignment, but I already know it is slightly out of wack because, on the hard, I can see the shaft is resting lightly on the shaft log. It seems to me that all I need to do is raise or lower the engine a little on the mounts. Anyone have any advice? I've never actually messed with this type of problem before.

The advice I've read is that course adjustments can be made on land, but fine adjustments should be made in the water. Raising the engine so the shaft is centered in the shaft log is the beginning. Once in the water, you'll need to unbolt the shaft from the flange and then use feeler guages to look for gaps. I think the rule of thumb is to try and get it within .001' for every inch of flange diameter.

shaft alignment The amount of deflection when on the hard compared with the amount of deflection in the water will vary by how thick your hull is. You don't say what boat you have. I would not even attempt it till it is floating for a couple of days. pigslo
It is a Catalina 27. The thing is I can see that it is touching the shaft log exit while it is out of the water. Wouldn't it be better to try it now while I can see the prop end rather than when it is in the water and I can't?
It is hard to figure while not there of course. If I were there.... I would first look to see how much the hull is deflecting in the stands. If it is touching the shaft log outside while on the the hard because of deflection due to the stands, then once it is in the water it is not going to be accurate any more when the hull goes back to the shape it is supposed to have. The second thing I would check (with feeler gauges) is the allignment right now and see if the alignment (whether high, low, left, or right) is consistent with what you see outside the hull. pigslo
Here's an idea, and a hopeful one at that. Maybe the shaft is touching the shaft log exit from deflection alone. The reason I say this is because there are no rubbing marks on the log from the shaft, which makes me think that perhaps in the water the shaft is aligned. Otherwise, I think there would be some sort of mark from the shaft rubbing against the log while under power.

Shaft alignment really should be done in the water. I'ts very difficult to ascertain that the boat is sitting true when on the hard. I've seen Cat27s that were severely flexed while sitting on cradle, so I'd really wait til you're afloat. The process itself is a bit complex as you have adjustments on all mounts (3 or 4 depending on installation) and you have few fixed references on the other end. You are working on several axes at once. While afloat you can still judge the "midpoint" of the shaft log by lifting the decoupled shaft and find the limits of motion, then block the shaft in the middle of that range. Then adjust the engine mounts to roughly match. This is followed by measuring the face to face distances at the coupling to get it the same all around. Initially this can be done with a piece of keystock, sliding it between coupling faces and set things up for the same fit (gap) everywhere. Feeler gauges can be used to get it more precise.
That is what I was alluding to, Jotun. While a bit complicated, alligning a shaft is mostly tedious and time consuming. It took me 4 hours to go from .065" out of allignment to .0015". Good luck. pigslo
The criteria is not the position of the shaft in the shaft log, but how the flange on the shaft mates with the flange on the engine. The shaft flange will be at right angles to the shaft to a high precision. If it mates with the engine flange then the engine and prop form a straight line and there will be a minimum of vibration. Remember you are trying to get the gap between the two flanges to vary by less than a couple of thousandths around the circumference. That is a pretty tight tolerance. Also when a boat is moved from stands on the hard to the water, it will take several days for it to completely reform to the new forces.
There are three steps to shaft alignment. 1. Center the shaft in the stern tube. Usually done with the coupling disconnected. The goal is to place the centerline of the shaft as close to the centerline of the stern tube/stern gland as possible. Concentricity is the goal. 2. Adjust the elevation and lateral position of the transmission output coupling flange by adjustment of engine and/or transmission mounts so that its centerline coincides with the shaft centerline and with coupling halves approximately matched for bolting together. 3. Bring the coupling halves together loosely and use a feeler gauge to check parallelism of the mating flange faces. (They must be clean.) Check in the vertical (12 o'clock and 6 o'clock positions) and in athwartship (9 o'clock and 3 o'clock) directions. Make additional adjustments (fine) to engine/transmission mounts as necessary. If significant adjustments are made, separate the flanges and repeat step 2 so that you don't disturb the position of the shaft centerline. 4. When flange faces are parallel within the limits specified by the engine maker, tighten all mounting bolts and check for parallel one more time. If problem found, repeat #3. 5. With all mountings secure and flanges parallel, install and tighten coupling bolts. This is a lot of work and it should be done when the boat is in the water so that it will assume its normal hull shape . Otherwise you may get to do it again. There is an option. You could get a flexible coupling and that will eliminate some of the really fussy work on the flange faces. You will still need to pay pretty close attention to the rest of it.
- ?
- 173.8K members
Top Contributors this Month

- Contact SDMC
- Vessel Selection Assist
- Pre- Purchase Guidance
- Building Your New Vessel
- Equipping Your New or Pre-Owned Vessel
- Boat Owner and Buyer Articles
- Testimonials
- Boat Buyers Gallery
- Captains’ Club
- Ready for Sea
- Refitting & Repairing Your Boat
- Vessel and Systems Inspection
- Boat Owners Gallery
- Industry Consulting
- Industry Articles
- Industry Gallery
- Educational Videos
- About Steve
- Upcoming Events
- Photo Gallery
- Travelogues
- Seaworthy and Challenges
- SDMC Lecture Offerings
- Sample Inspection Reports
- SDMC Webinar Lecture Series

- Feature Article
- Marine Systems Excellence eMagazine
The Ins and Outs of Shaft Alignment Part II
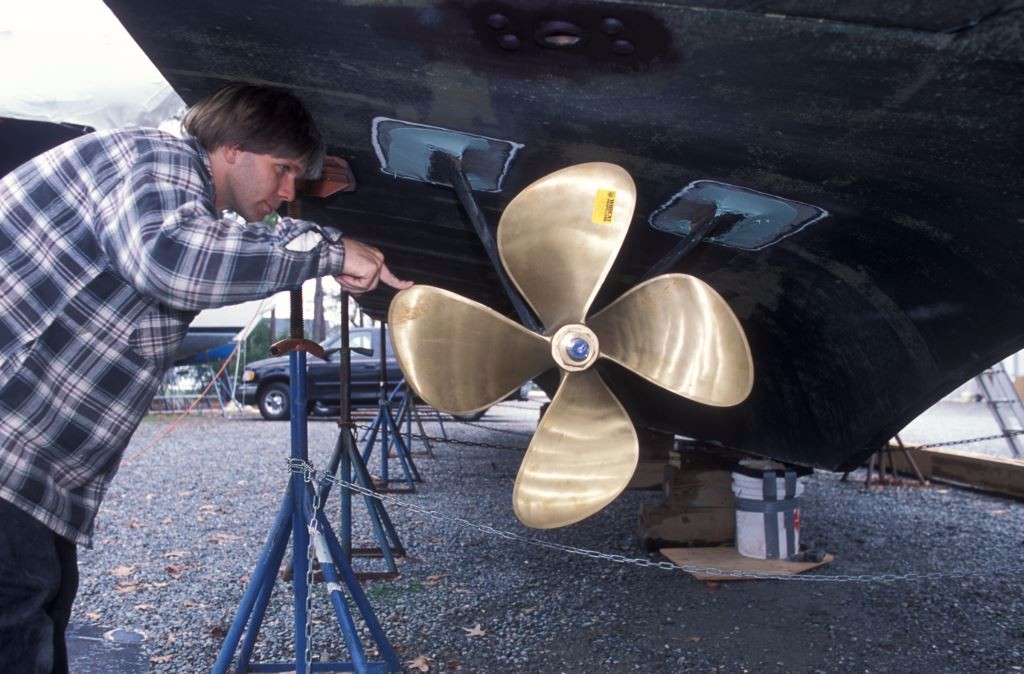
Text and photos by Steve D’Antonio
Copyright © 2016
From the Masthead
A few days ago I completed an article for a boating magazine, in which I offered advice for those attending upcoming boat shows, covering, among other things, the standards to which boats are built. Doing so reminded me of the importance of this subject, and just how much misunderstanding surrounds it.
In a discussion with a client recently, regarding an inspection I carried out aboard his four year old vessel, he said, “I’m surprised at the number of electrical faults, nearly all of which seem to have been there from the start. What were the standards when it was built?” In a world where so much is governed by standards, automobiles, aviation, building construction and commercial shipping, my response no doubt came as a surprise to him, as it does to so many boat owners, “There were no [electrical] standards in effect when the vessel was built, and there are none today, at least none that US boat builders, and repair yards, are required to follow by law”. Where construction details are concerned, specifically electrical, fuel and ventilation systems, only gasoline-powered vessels are required to meet a set of guidelines, laws if you will, set forth in the US Code of Federal Regulations. With the exception of those governing navigation lights, fire extinguishers and a few others, recreational, diesel-powered vessels are exempt from these requirements.
Therefore, the onus is on boat builders and boat yards to follow voluntary standards, which include those established by the American Boat and Yacht Council (ABYC). Hardly a day goes by where I don’t look up, cite, recommend or reference one of these standards, contained in the voluminous, ‘Standards and Technical Information Reports for Small Craft’. The value of these standards, and the manner in which they’ve raised the quality, reliability and safety bars within the marine industry, cannot be over stated. There’s more to the story, however; so I’ll alert readers when the full article is published and available on line.
For now, here’s a preview. What does this mean for a boat buyer, new or used? If you are considering a new boat, be certain to ask the broker if the builder belongs to ABYC (you can confirm membership on ABYC’s website), and if so, does the vessel comply with ABYC Standards, and if so, which ones? There are over 60. It’s rare to encounter a builder today who is not a member of ABYC, but if you do it’s cause for concern. If the builder indicates compliance with some or all relevant ABYC Standards, confirm this with a pre-purchase survey before closing the deal. Yes, even new boats should be inspected. For used vessels, its condition should be evaluated on several levels, including ABYC compliance. I often hear sellers say, “It met the standards when it was built, why does it need to meet current standards?” The simple answer is, a short circuit, fire, carbon monoxide leak, electrocution hazard or fuel leak can’t read the standards, it doesn’t matter what was acceptable at the time of construction, if it’s unsafe, it’s unsafe. Finally, anyone carrying out work on your vessel, service, repairs or modifications, new or used, should agree to do so in compliance with current ABYC standards ( http://www.abycinc.org )
This month’s Marine Systems Excellence eMagazine feature, part two of a two part series, continues our look at running gear alignment. I hope you find it both useful and interesting.
The Ins and Outs of Shaft Alignment – Part II
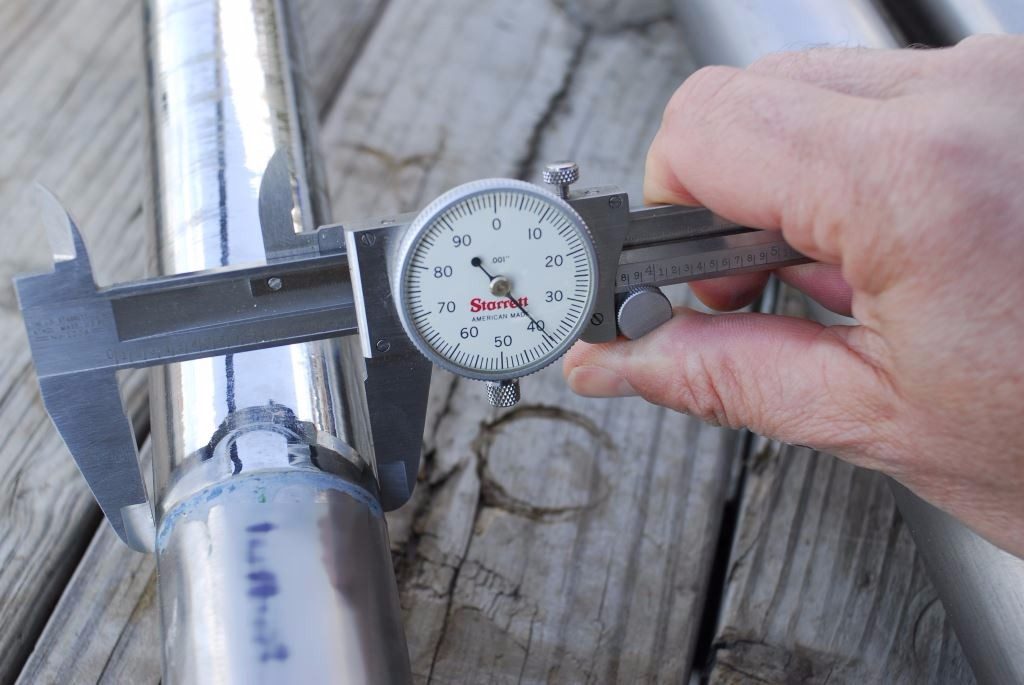
Bearing misalignment can lead to both bearing and shaft wear. The maximum tolerance for shaft wear is just one thousandth of an inch. The shaft shown here has been condemned as a result of excessive wear, caused by gross misalignment.
In last month’s column I reviewed the importance of, and techniques for, ensuring proper engine alignment. That is, the alignment between the engine and the propeller shaft. In the second and final part of this series we’ll review shaft alignment.
Nearly all marine engines are designed to be adjustable, to a point, relative to the propeller shaft, using adjustment or jacking nuts on their motor mounts. The adjustment should be thought of as no more than fine tuning, the maximum range of vertical travel being limited to no more than an inch or two at the most, which is considerable when one considers that alignment is typically measured to just a few one thousandths of an inch. Thus, the responsibility rests with the naval architect and boat builder to ensure that the design and execution of the engine installation guarantees near perfect alignment with the shaft before the motor mounts are adjusted.
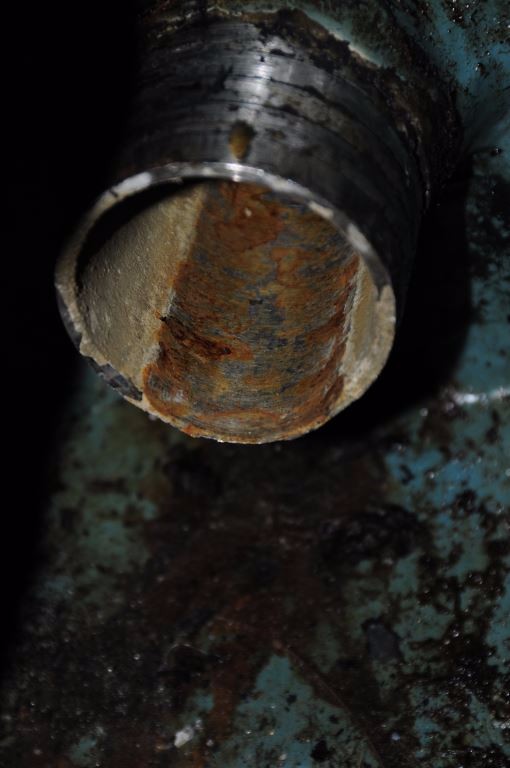
These shaft logs show signs of wear caused by improper shaft alignment. Contact of this sort can lead to increased fuel consumption, vibration, heat generation and eventually flooding.
The Other Alignment
There is another side to the alignment story; it involves the support and position of the propeller shaft relative to its bearing(s), the shaft log and the engine. While engine alignment is, or is expected to be, well understood by most marine industry professionals, shaft alignment is, on the other hand, far more esoteric and well understood by fewer folks in the industry. In my experience, precious few truly understand its importance, and the consequences of misalignment, and fewer still understand the techniques and processes involved in making adjustments and corrections.
Interestingly, and contrary to popular belief, shaft misalignment rarely leads to vibration, as the bow or offset induced in a shaft by misaligned bearings is constant. If, on the other hand, as a result of misalignment, the shaft makes contact with the shaft log, more on what that is in a moment, it may lead to vibration. Improper shaft alignment can lead to excessive shaft drag, and the resultant increase in fuel consumption, and accelerated bearing and shaft wear.
A few years ago I inspected a vessel while it was hauled out. When I came to the propeller I made an unsuccessful attempt to rotate it, to gauge the condition of the bearings and alignment. Regardless of how hard I tried, I was unable to rotate either shaft on this twin screw vessel 60 foot vessel. This is a clear indication of either severe shaft misalignment (as opposed to engine misalignment, which rarely imparts this sort of resistance) or, less commonly, swollen shaft bearings. While final alignment of an engine to its shaft should only be carried out while a vessel has been afloat for some time, even when hauled out the shaft should turn without undue effort once adhesion between it and its bearings is broken. In this case, even when hanging on a propeller blade I was unable to budge these shafts. Clearly, this vessel was in need of a shaft and bearing alignment analysis.
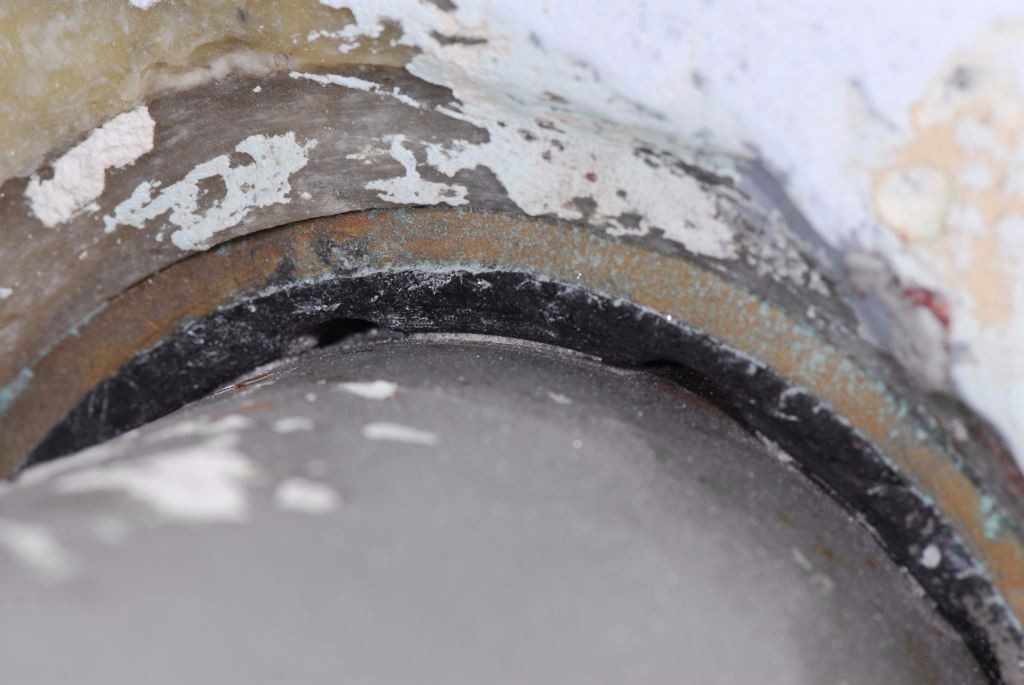
Misalignment can make shafts difficult to turn, however, so too can swollen bearings. That possibility should be explored as part of any analysis of a shaft that is difficult to turn.
How Shaft Bearings Work and are Supported
In virtually all cases, propeller shafts are supported by one and sometimes as many as four, for longer shafts, bearings, often referred to by their trade name ‘Cutless® bearings’. Shaft bearings are tubular pipe-like components, the outer shell of which is typically made of brass, and sometimes a fiberglass-like material (the latter is designed to be used on steel and aluminum vessels, to avoid the corrosion potential caused by copper alloys like brass), with an inner liner of grooved or fluted rubber. It comes as a surprise to many users that the sole source of lubrication and cooling is seawater; if water flow to the bearing is insufficient or if it’s interrupted by marine growth on the shaft or clogging of a shaft log water injection system, rapid bearing wear can ensue.
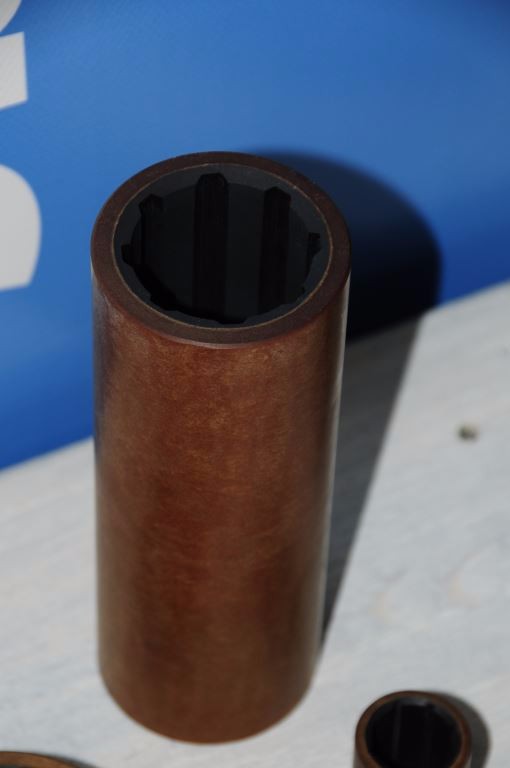
Shaft bearing shells are typically made of brass (above), however, non-metallic versions (top), are available, which are often used in steel and aluminum struts to avoid galvanic corrosion.
Shaft bearings may be found in and supported by struts, I or V shaped metal supports attached to the vessel’s hull, through which the shaft passes, and/or embedded within the shaft log, in the keel or hull. When the vessel is built, the builder must make a concerted effort to ensure that bearings are properly located to support the shaft, while ensuring that they are also aligned with the theoretical shaft’s centerline, a line that is perpendicular with, and begins at the center of, the transmission output coupling, and travels aft through the bearing(s). The line must also be centered in and parallel with the bearing(s). If the builder is successful in ensuring this alignment, barring groundings or other damage, it should remain correct throughout the life of the vessel. While small adjustments may be made to the relationship between the engine and shaft, by adjusting the location of the former, the shaft’s relationship to and alignment with the bearings should remain constant.
Analysis and Adjustment
In practice, it’s not uncommon to encounter shafts and bearings that are misaligned, and the greater the number of bearings, the greater the likelihood of misalignment. While shaft to bearing alignment can be challenging, aligning a shaft to several bearings, as well as the general location of the engine, can be daunting. As such, it’s easy to see how this process can go awry while the vessel is being built.
Traditionally, during construction or repairs, the process begins with a length of small diameter yet stout string or wire, which is glued to the center of the transmission output coupling. It is led aft, through the hole through which the shaft passes, the shaft log, and out the vessel’s stern section, where it is anchored, typically to a weighted object like a jack stand. Using this string or wire as a reference point, bearings and, if present, struts are positioned. When properly aligned, the bearing(s) must remain centered on and parallel with the string or wire.
While this traditional approach is still used, more modern tools are now routinely employed; these include lasers and optical sights, both of which were mentioned last month. Using a laser or sighting tool, an installer can, with a great accuracy, position one or more bearings along the sight line. While this aspect of shaft alignment is critical, it’s the easy part. Setting the bearings in place, permanently, can be more challenging.
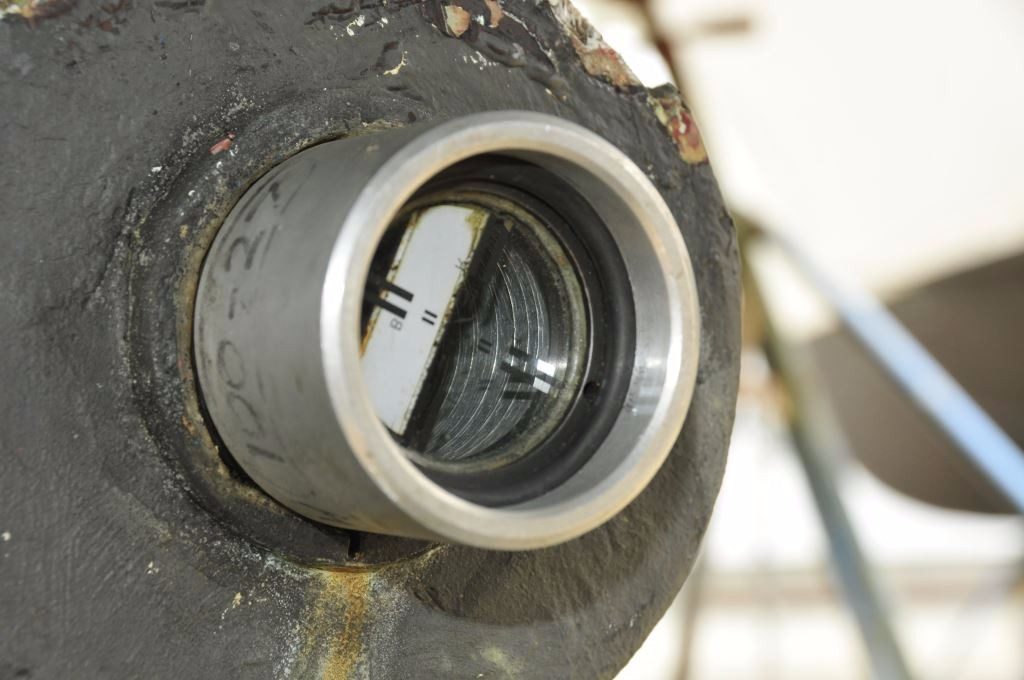
Bearing alignment can be analyzed using either optical (top) or laser (above) sighing equipment. This alignment method eliminates the need for string or wire and caliper measurements.
Initially, the strut or bearing is “dry fit”. That is, it’s positioned roughly to determine what needs to be done to align it with the shaft. The process typically involves a technique known as casting. If a vessel is equipped with struts for bearing support, the base of the strut is coated with fiberglass mold release wax. It is then set into a mixture of thickened, reinforced epoxy and positioned so that it remains centered on and parallel with the string, laser or optical sight or shaft line. The strut is “hung” from support fasteners and wedges are used to adjust its height and orientation to the shaft centerline. Once the position is set, the epoxy is allowed to cure, after which, thanks to the mold release wax, the strut is removed. Wax is removed from the strut and the epoxy surface, and the strut is then set in polyurethane bedding compound, ensuring a watertight seal with the hull. In some cases, the bearing centerline may be below that of the shaft. In this instance, depending on the degree of misalignment involved, a recess may have to be made in the hull, to accept the strut’s base, the strut may require modification or a new strut may need to be manufactured all together.
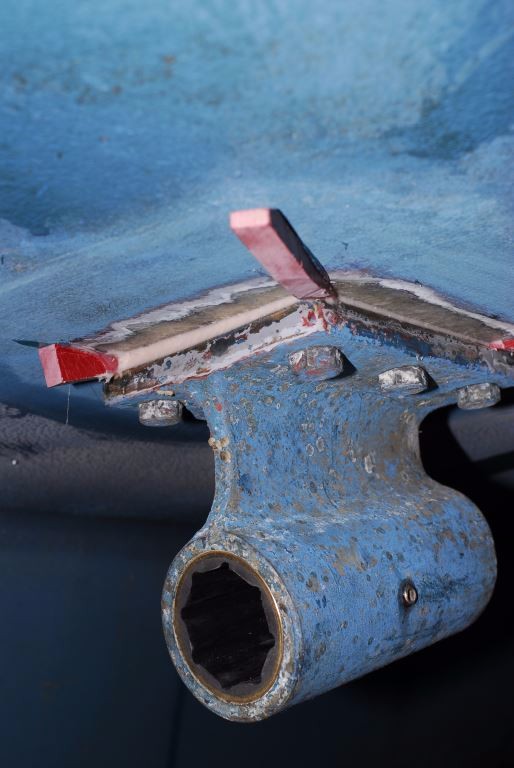
Struts are typically repositioned, to achieve proper alignment, using thickened epoxy as a shim. Wedges are temporarily inserted to adjust placement.
A similar process is employed for bearings that reside within the shaft log, and strut. The bearing itself is waxed and set in epoxy; wedges are used to position it so that it remains parallel with and centered on the shaft line until the epoxy cures. All bearings should be a light press fit in the shaft log or strut. Ultimately, bearings are retained using set screws, a minimum of two must be used, they should be installed at 60° to each side of the bottom centerline, or at the 4 o’clock and 8 o’clock positions (alternately, they may be installed at the 3 and 9 o’clock positions, but not above the propeller shaft centerline). Set screws must be harder and galvanically noble to the bearing shell; indentations ( not holes) should be drilled into the bearing shell, using a drill bit whose tip angle matches that of the set screw, which the set screws engage. A thread locking compound should be used on set screw threads.
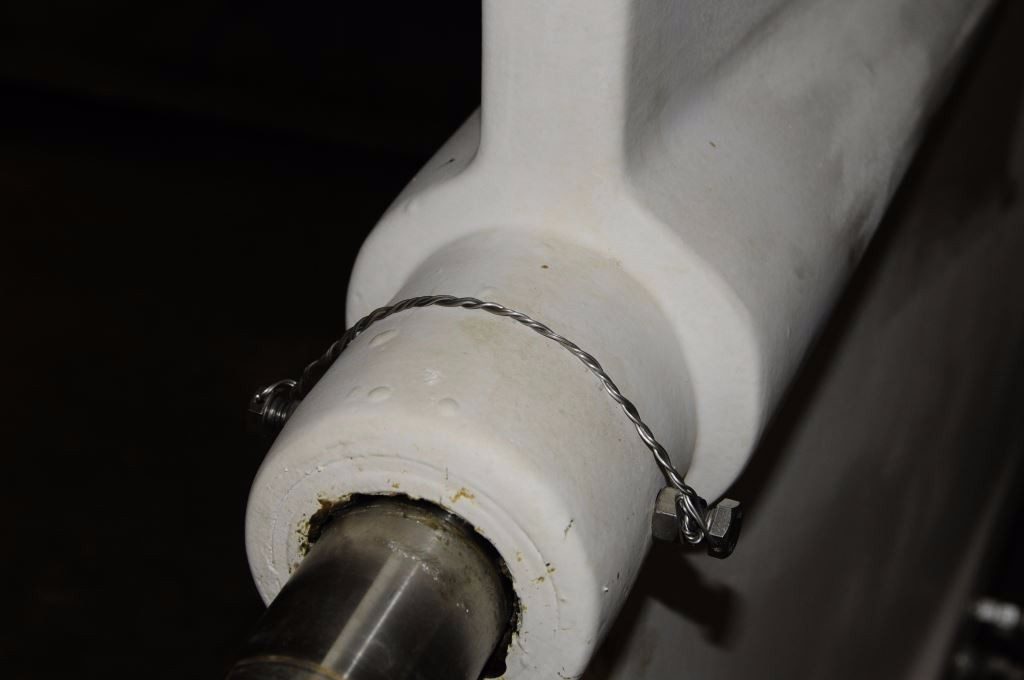
Shaft bearings must be retained with set screws. Here, two screws , retained with seizing wire, are installed at the three and nine o’clock positions.
Ultimately, once the shaft to bearing alignment is complete, even a large diameter, long shaft should, with the benefit of nothing more than light lubrication from soapy water, rotate with little more effort than is required to lift an overhead garage door.
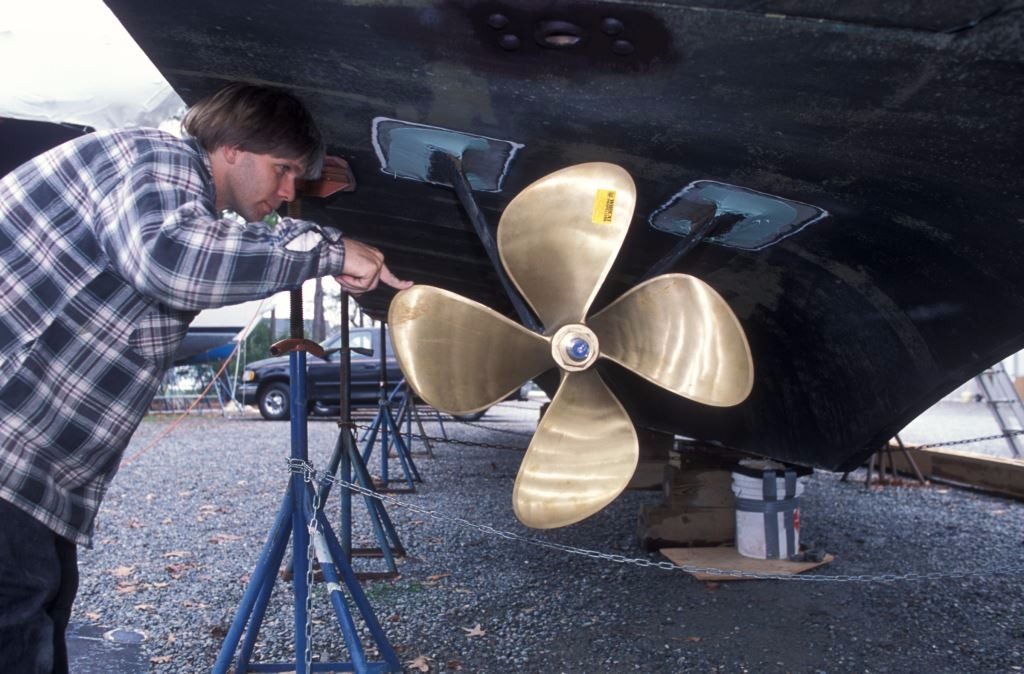
When properly aligned, propellers and shafts should turn with relative ease.
Before entrusting your vessel to anyone for shaft alignment analysis or adjustment, carefully scrutinize their knowledge and experience on this all too important, yet frequently misunderstood, subject, and ask for references as well.

You cannot copy content of this page
Log in or Sign up
You are using an out of date browser. It may not display this or other websites correctly. You should upgrade or use an alternative browser .
How to align this prop shaft
Discussion in ' Inboards ' started by holdfast , Mar 17, 2014 .

holdfast Junior Member
Hello, I have to align the propeller shafts on this boat. It is a little bit more complicated than usual as each shaft has four supporting points. There are two bushins outside the hull (as you can see in the picture), the shaft gland, a ball bearing and another thrust bearing before the Aquadrive system. I don't really know wich of the supporting poins is in the right position yet. I'm planning to do it with a laser, any advice please is allways helpfull. Cheers.

michael pierzga Senior Member
The first strut..p bracket ....will be trouble. How is it mounted in the hull ? Is it adjustable, shims, set into chockfast or epoxy Are there three cutlass bearings ? I believe the rule for distance between shaft bearings is 30 times diameter. Your shaft looks long and thin.

gonzo Senior Member
The struts were there already, so unless the hull had some structural damage, they should be OK. The engine should be aligned in the water after the hull swelled up. Planked boats get loose when dry and change shape. The fastener pattern shows it is either double planked or seam battened which minimized the problem.
Possible that wood boats change shape. Be careful that the aft jackstand its not deforming the hull. Have a carefull look when you pull the shaft.
Thanks Michael anf Gonzo for your replies. I attach some pics of the seal, the ball bearing and the thrust bearing. We are going to change the seal and the ball bearing and of course the bushings from the struts. The whole shaft needs to be aligned from 0 as it is not perfectly centered. I have installed new engines and there is no way to aligned them up with the engine mounts adjusting margin. Now the engine mounts are all the way to one side and they are still not aligned. My concern is if the struts need to be adjusted, it is going to be very difficult as the haven't been taken apart for ages. Are you sure the boat changes the shape after less than one month out of the water or with the jackstands? I know is made of wood but it is pretty solid too! I was planing to do all the job in the shed and I think there is no other choice except leaving the enging alignment after the launching... I think the starting point is to put the engines in the center position of the mounts, try to align the shaft betweeen there and the aft strut, wich I will have to check if it's in the right position too (I don't know how yet..) I will keep you updated, any advise allways help Cheers. [/IMG]

PAR Yacht Designer/Builder
This is a pretty critical aspect of a new engine install, so if you're having difficultly with the associated problem solving necessary in these type of upgrades, you'd be best advised to hire someone that has a few dozen installs under their belt to help. Basically, you just can get it close, while on the hard and you fine tune to a few thousands of an inch, once she's taken up. Anything less than this will insure issues, once underway.
Hard to see what your engine installation looks like. It would be much easier to move the engine into the shaft run , rather than reseat all the struts and bearing and bring the shaft to the new engine position. Chances are that your p bracket setup is reasonably well aligned Saddle bearings are easy to shim and adjust. If some misalignment is found in your P bracket Setup it may be easiest to adjust the saddle.
- Advertisement:

CDK retired engineer
The shaft alignment is simple and can be done without special equipment. Once the shaft is removed and new cutlass bearings in place you could use a laser to check the alignment, but when you push the shaft back in, you certainly feel if one of the bearings is off center. The engine is a different matter, because even with a laser you can only align in one plane and there may still be an axial angle.

Dialing in an alignment on a v-drive

Single engine, dual independent props for cat?

Advice on how to convert inboard jet drive boat to propeller....


Inboard Prop Shaft Thrust Bearing/Mount & Hydraulic Get Home

initial vibration of inboard prop when put in fwd or rev

Prop thro transom
Here's one i have not heard...how close should my prop be to my rudder.

Help with stern tube/propshaft design

New prop shaft coupling with new shaft

Propulsion for passagemaker
- No, create an account now.
- Yes, my password is:
- Forgot your password?


- CREATE AN ACCOUNT
- Boat Cover Finder
- Bimini Top Finder
- Boat Propeller Finder
- Engine Parts Finder
- Anchor & Dock
- Watersports
- Clothing and Footwear
- Engine Parts
- Cabin and Galley
- Covers and Biminis
- Electronics
- Paint and Maintenance
- Pumps and Plumbing
- Anchor Chains & Ropes
- Boat Fenders
- Boat Mooring
- Boat Protection
- Dock Storage & Protection
- Ladders, Steps, & Platforms
- Top Sellers

- Fishing Rods
- Fishing Reels
- Fishing Rod & Reel Combos
- Fishing Tools & Tackle Boxes
- Fishing Line
- Fly Fishing
- Fishing Bait & Fishing Lures
- Fishing Rod Holders & Storage Racks
- Fish Finders, Sounders & Sonar
- Trolling Motors
- Fishing Nets
- Fishing Downriggers & Acessories
- Fishing Outriggers & Acessories
- Fishing Kayaks
- Fish Cleaning Tables

- Inflatable Rafts
- Paddle Boarding
- Paddles & Oars
- Wakeboard, Wakesurf & Ski
- Wakeboard Towers
- Tow Ropes & Handles
- Life Jackets & PFDs
- Snow Sports
- Roof Racks, Carriers, Dollies

Men's Clothing
- Accessories
Men's Footwear
- Atheltic Shoes
- Water Shoes
Women's Clothing
- Dresses & Skirts
Women's Footwear
- Fuel Systems
- Sacrificial Anodes & Zincs
- Generator Parts
- Inflatable Boats
- Propeller Parts & Accessories
- Boat Manuals
- PWC Parts & Accessories

- Fishing Boat Seats
- Offshore Boat Seats
- Ski Boat Seats
- Pontoon Boat Seats & Furniture
- Boat Seat Pedestals & Hardware
- Boat Seats by Manufacturer
- Boat Tables & Hardware
- Boat Seat Covers
- Boat Seat Vinyl
- Floating Boat Cushions

- Barbeque Grills
- Boat Drink Holders
- Cabin Accessories & Hardware
- Boat Ventilation
- Interior & Cabin Lighting
- Marine Teak Products
- Carbon Monoxide & Smoke Detectors
- Binoculars & Telescopes

Boat Bimini Tops
- Bimini Top Accessories
- Pontoon Bimini Tops
- Other Biminis
- RV & Trailer Covers
- Boat Shrink Wrap & Accessories
- Boat Shelters
Boat Covers
- Boat Cover Accessories
- Boat Lift Canopy Covers
- Other Covers
- Boat Wiring & Cable
- Marine Batteries & Accessories
- Marine DC Power Plugs & Sockets
- Marine Electrical Meters
- Boat Lights
- Marine Electrical Panels & Circuit Breakers
- Power Packs & Jump Starters
- Marine Solar Power Accessories
- Marine Electrical Terminals
- Marine Fuse Blocks & Terminal Blocks
- Marine Switches
- Shore Power & AC Distribution

- Marine Audio & Video
- GPS Chartplotters & Accessories
- Electronic Navigation Charts & Software
- Digital Instruments
- Display Mounts
- VHF Radios & Communication
- Marine Radar
- Auto Pilot Systems
- Action Cameras

- Fiberglass & Epoxy Boat Repair
- Boat Paint & Varnish
- Marine Adhesives, Sealant, & Caulking
- Marine Engine Maintenance
- Boat Cleaners & Waxes
- Boat Cleaning Supplies

- Fresh Water Boat Systems
- Bilge Pumps
- Marine Plumbing Parts
- Wash Down Pumps
- Livewell Aerator Pumps & Live Bait Wells
- Toilet & Waste Pumps
- Marine Pump Replacement Parts

- Tires, Rims, & Hub Kits
- Boat Trailer Winches
- Boat Motor Supports & Transom Savers
- Boat Trailer Guides & Rollers
- Boat Trailer Fenders
- Boat Trailer Lights
- Boat Trailer Hardware
- Boat Trailer Jacks
- Boat Trailer Brakes & Axles
- Boat Trailer Tie Downs
- Couplers, Mounts, Hitches, & Locks

- Boat Deck Harware
- Marine Nuts, Bolts, & Screws
- Boat Handles, Pulls, & Rings
- Prop Nut Kits & Hardware
- Boat Cabin Hardware
- Marine Fasteners
- Boat Windshield Parts
- Boat Tubing & Rails
- Boat Mirrors
- Marine Tools & Tool Kits
- Boat Lettering

- Women's Clothing Deals
- Men's Clothing Deals
- Fishing Deals
- Anchor & Dock Deals
- Electrical Deals
- Electronics Deals
- Paint & Maintenance Deals
- Pumps & Plumbing Deals
- Boat Seats Deals
- Trailering Deals
- Camping & RV Deals
- Dealer Login

- Forums Login

- Search forums
- Boat Repair and Restoration
- Boat Restoration, Building, and Hull Repair
Prop shaft alignment
- Thread starter J. Mark
- Start date Apr 14, 2009
Petty Officer 1st Class
- Apr 14, 2009
Working on rebuilding a true inboard. I have read the prop shaft alignment guide from Borg Warner and they are very specific and the tolerances are .003 of parallel between the output shaft and the prop shaft couplers. To align, the engine has to be moved at all 4 corners. The motor mounts allow up and down adjustment via a sandwiched nut arrangement . . . but the motor mounts also use a locking shim to keep the lower nut from turning once it is set. Am I correct in assuming I need to bend these flat to set the alignment and once I am done bend them back to lock the lower nuts in place? The specs call for the final adjustment to be done with the boat in the water. To turn the nuts I need to lift weight off of the engine and I don't see how to do that with the boat in the water. Are these specs overly rigid? I don't imagine boat manufacturers put every boat in the water for final adjustment, but if I need to, I will. If you have reinstalled an inboard set up I'd like to know how you did it and your thoughts on the process. Thanks

Re: Prop shaft alignment I have done a number of inboard installations. Yes, .003" is the maximum recommended allowance (closer is better). Can you be farther off than this(?), sure, but it will result in more vibration and more bearing wear in both the cutlass bearing in the strut and in the reverse gear. How much more (?), depends on how far out of alignment it is, a bit out & it may not cause an issue for as long as you own the boat, to far out & you might be replacing parts every couple of years. I'm not familiar with the 'locking shimes' you are describing, but by your description I'd say you are right on. As for lifting the engine to make the adjustment, that is not necessary. Unless there is a problem you should be able to turn the bottom nuts quite easilly with a wrench without lifting the engine. When you are done with the alighnment there should be pretty much even weight on all four bottom nuts (equal difficulty to turn), and then you tighten the top nuts. You didn't say how large the boat is, which will affect the need to re-allign after launching. The smaller the boat the less the issue. If the boat is blocked up well you should not have a problem. At the very least I would recommend pulling the flange bolts a day or so after launching and checking the allignment (chances are pretty goo it will be fine).
Re: Prop shaft alignment Thanks Ned, it is a 19 foot Marlin Ski boat. I know I need to be close and intend to be dead nut on if possible. My front motor mounts have sliding pins (as do the rears) that are frozen in place. I'll pull them off and get them freed up before I try and align things. When I got the boat the alignment was so bad that the bottom of the shaft log was eaten away. Hopefully I can do better than the PO!
- Apr 15, 2009
Re: Prop shaft alignment I'll post an update in my restore thread when I get it done. http://forums.iboats.com/showthread.php?t=292744

Professional BoatBuilder Magazine
Running gear alignment.
By Steve D'Antonio , Nov 4, 2010
Tips on adjusting the engine, bearings, and shaft for maximum efficiency
Laser alignment assures the correct location and articulation of a shaft bearing.
Many consider running-gear alignment to be a black art. At a yard I once managed, I clearly recall watching a contractor, who specialized in this work, take a decidedly seat-of-the-pants approach to “calculating” shaft weight and the associated sag or droop.
When it comes to ensuring that an inboard propeller shaft and its supporting bearings are properly installed and aligned, there might be some art, but there’s no magic. The practices and procedures are straightforward, and if you take care to ensure accuracy and precision, the results should be predictable.
There are essentially two types of alignment. The first is positioning the engine relative to the shaft. The second is more difficult: adjusting the shaft bearings and/or their supports.
Engine Alignment Engines and motor mounts are designed to accommodate some adjustment. Most mounts employ jacking screws that allow for a narrow-range change of elevation. Side-to-side adjustment is often facilitated by the mount’s elliptical-base fastener holes—again, with a limited range.
In this type of adjustment the engine is moved relative to the position of the shaft, because the shaft’s position is assumed to be nonadjustable. Unless the installation includes a thrust bearing of some sort, all the thrust created by the propeller is transmitted to the vessel’s hull via the motor mounts. The boat is pushed through the water by virtue of the mounts and their associated hardware. Keep this in mind as you select and install components.
Because you should tighten all fasteners with a torque wrench, avoid thin fender washers that are easily distorted when you install mounts. Likewise, through-bolts, locking nuts, and machine screws should be favored in place of self-tapping lag screws. Because of the pressure and leverage imparted on motor mounts, installers and those performing adjustments should avoid maximum extension of the mount’s adjustment screw thread, which could cause cyclical loading-induced failure. If more of the mount’s adjustment screw threads are visible under the engine support bracket than on top of it, a shim should be installed beneath the mount’s foot plate to close the gap. Ideally, when adjustments are complete, the engine bracket should rest somewhere in the middle of the adjustment stud. Shim material should be rugged, incompressible, and resistant to splitting or fracturing. Steel or aluminum plate works well; prefab FRP such as GPO or G10 is also suitable. Avoid high-density polyethylene, including King Starboard and other non-reinforced plastics.
Coarse adjustment of this motor mount was performed with a composite shim.
The face of the transmission output coupling and the face of the propeller shaft coupling must be parallel, or made parallel, to within no more than 0.004″, or 0.1mm (rules of thumb for this calculation vary; the stated figure is from a shaft manufacturer). Inspect the faces for damage, scoring, corrosion, dents, and distortion of any sort. Any irregularities will make it difficult, if not impossible, to measure for alignment analysis.
What’s often not well understood about alignment is the requirement that the theoretical centerline of the shaft to be centered on the transmission output coupling.
Shaft Alignment Yard personnel often ask, “How difficult should it be turn a shaft and prop when the vessel is blocked?” I know a shaft that’s too tight when I encounter one, but that’s not a helpful answer to others making a determination whose results could lead to costly repairs.
Here’s a rough rule of thumb that I go by: provided the vessel is properly supported, and the bearings are lubricated with diluted dishwashing detergent, even large shafts—say 2.5″ (63.5mm) in diameter, 18′ (5.5m) long, and supported by three bearings—should move with no more effort than an adult can impart with one hand. That’s subjective to be sure. Recently, I was able to lift my entire body weight off the ground in an attempt to turn a 3″-diameter (76mm) by 18′-long two-bearing shaft installation. Clearly it was too tight, and the bearings and shaft likely needed realignment.
Shaft alignment is typically thought of as nonadjustable. As mentioned earlier, that’s not strictly true. When the shaft supports, strut, or keel/shaftlog-mounted cutless bearings are installed, their position should be carefully chosen to ensure that they are parallel and share the same theoretical shaft centerline . If the bearings are not aligned with each other, if they are not parallel, or if they deviate from the shaft centerline, the shaft and/or bearings will be distorted during installation. The classic pinched bearing is an indication of that, as is the shaft that’s exceptionally difficult to turn from the propeller end. The distortion induces a range of maladies, including excessive bearing and shaft wear, vibration, increased drag, and diminished fuel efficiency and performance.
If the bearings are not properly aligned with the shaft at the time of initial construction or installation, then they or their supports, the struts, shaftlog- or keel-mounted bearing(s), must be repositioned. While this wouldn’t strictly fall under the definition of “adjustable,” modifying the position of these bearings becomes the only means of resolving the misalignment. So, shaft alignment is adjustable, but not easily.
I’ve supervised many shaft and support realignments. While there are several methods, my preference is to begin by assessing the misalignment with a laser alignment tool. The full procedure is beyond the scope of this article, but in short: by placing a laser in the aftmost cutless bearing, with the shaft out, and pointing it toward the engine, you can determine, with purpose-made targets, if the aftmost bearing and any intermediate bearings are properly aligned. The laser pinpoint should land in the middle of the transmission output coupling as well as the targets placed in any intermediate bearings, confirming that the theoretical shaft centerline is aligned with the output coupling centerline.
Engine alignment also can be confirmed by installing the laser in the coupling shaft bore and shining it aft to targets placed in the bearings. A final engine alignment must still be confirmed by coupling clearance measurement after the vessel has been launched and running gear components have settled.
Yards that routinely confirm or adjust shaft alignment typically make or have made a series of targets and jigs to support and aim lasers through and onto a variety of bearing and coupling sizes and types.
Bearing Relocation If a bearing is out of alignment, from either a centerline or parallel point of view, it must be adjusted. If the bearing is strut-mounted, the strut must be removed and a base wedge of cast epoxy or fabricated FRP installed to relocate the bearing. Again, repositioning is confirmed with a laser and target. The strut must be held firmly in place, with the laser on target, until the epoxy cures. Afterward, the waxed strut is removed, cleaned, and bedded and fastened in place. If the bearing is mounted in a keel or shaftlog, the process can be more challenging; however, casting in the realigned position remains the order of the day. In some cases, a section of shaft can be used to align both ends of a keel- or shaftlog-mounted bearing during the casting process.
This strut was shimmed to reposition the bearing.
A final variable to consider is shaft sag. The shaft section that lies between the forwardmost bearing (in a multiple-bearing installation) and the coupling will droop or sag under its own weight and the weight of the coupling. If the droop is not corrected before the shaft and transmission couplings are aligned, then a bow, or curve, will be built into the finished assembly.
If you’re skeptical of just how much a shaft can droop, allow the length of shaft from the bearing to the transmission, with the coupling installed, to hang off a sturdy workbench or table. Then measure the difference between the distance from the floor to the shaft at the table and the floor to the shaft as it enters the coupling. The result is the droop.
Sag can be factored out by aligning the centerline of the transmission output coupling with a laser shot from the cutless bearing. If a laser shaft alignment has not been carried out, and if the shaft has not been removed, the droop can be negated by calculating the weight of the unsupported shaft (shaft weight data is available from all shaft manufacturers; one example is http://www.wbmetals.com/faqs.asp#Tip11 ), dividing that by 2 (because one end of the shaft is supported), adding the weight of the coupling, and then lifting, or “neutralizing,” the weight using an industrial hanging scale or compression scale under the shaft.
Applying a calculated lift can offset shaft sag while aligning running gear.
For example, 4′ (1.2m) of 2″ (51mm) shaft weighs 42 lbs (19 kg), divided by 2 is 21 lbs (9.5 kg), plus the weight of the coupling—which we’ll say is 22 lbs (10 kg)—equals 43 lbs (19.5 kg). Lifting 43 lbs at the coupling end of the shaft will negate the effect of the droop. In practice, the droop is negligible for small-diameter shafts and for shafts whose unsupported overhang is comparatively short, making the above procedures unnecessary. For long spans and heavy shafts/couplings, those steps are worth the effort.
Roughly one-third of the new vessels I encounter suffer from some form of shaft misalignment—either misaligned bearings or shaft droop. The next time someone mentions checking alignment, take a moment to discuss exactly what’s meant and what’s involved in ensuring alignment is right in every respect.
Read more Systems articles
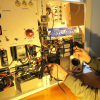
- Learn Electrical Systems from Nigel Calder
Have you’ve ever wished you could immerse yourself in one of contributing editor Nigel Calder’s Professional BoatBuilder articles about onboard systems and ask him questions at the end of every… Read more »
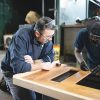
Marine Trade Education News
Ferretti Group Adds Trade Schools The Italian luxury yacht builder, who owns upscale brands such as Riva, Ferretti, Italma, CRN, Wally, and Pershing, announced the opening of marine trade schools… Read more »
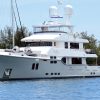
Life Raft Installation
Installing a life raft is straightforward but easy to get wrong—with dire results.

Recent Posts
- SNAME Powerboat Symposium Is Back
- Candela’s Faith in Foiling Ferries
- Australia II Wing Keel Controversy – Part 2
- Australia II Wing Keel Controversy – Part 1
- Companies (83)
- Construction (105)
- Design (160)
- Drawing Board (10)
- Education (25)
- Environment (16)
- Events (21)
- Materials (49)
- Obituary (17)
- People/Profiles (48)
- Products (16)
- Propulsion Systems (32)
- Racing (16)
- Repair (37)
- Rovings (315)
- Short Cuts (3)
- Sponsored Partner News (13)
- Systems (80)
- Task Sheet (1)
- Uncategorized (26)
- Wood to Glass (7)
ProBoat.com Archives

- David Pascoe
- All Articles (over 180)
- Mid Size Power Boats
- Buyers' Guide to Outboard Boats
- Surveying Fiberglass Power Boats (2E)
- Marine Investigations
- Domestic (USA)
- International
- Privacy Policy
- All Articles
- Order Books

- Boat Reviews
- Buying a Boat
- Cores & Structural Issues
- Marine Engines
- Maintenance & Repairs
- Hull Blisters
- Marine Surveying
- Insurance Issues
- Boat Handling & Boat Safety
- Hurricane Preparations
- Fuel Issues

Read Online
Full Chapter One
Troubleshooting Problems
Involving engine/shaft alignment, by david pascoe.
When it comes to yacht maintenance, one of the least understood and most overlooked systems that require maintenance, engine and shaft alignment probably heads the list.
Table of Contents - Show/Hide
Damages caused by engine/shaft misalignment, reasons causing damages, how to check your system, dial indicating shafts, weak struts.
Here's a short list of the problems associated with incorrect alignment and poor or worn out engine mounts:
- Rapid bearing wear.
- Causes stuffing boxes to wear out and leak, not infrequently sinking the boat.
- Bent or broken shafts
- Drive system vibration that can damage transmissions, engine mounts and the boat hull itself.
- Transmission failure caused by increased stress on the rear output shaft bearings and gears.
- Loosening of struts, causing leaking and possible sinking.
- Oscillating propeller shaft causing stuffing box clamps to loosen and work free, usually sinking the boat.
- Wear or worn out engine mounts cause drive shaft misalignment to stern drive, causing universal joints to oscillate and wear out.
These are but a few of the damages that can be caused by basic engine/shaft misalignment. Now comes a discussion of why, unlike in an automotive applications, boat engine drive systems do not indefinetly remain in alignment and need to be periodically checked and realigned. People tend to think of boats and yachts as being rigid structures, but they're not. The fact is that boats bend and twist in all directions, albeit not to any degree that's visually detectable. Expecially fiberglass boats, because they are a thermosetting plastic, can change their shape over time. This can happen either as a result of improper hauling and shoring, or it can happen simply as a factor of age and the effects of gravity.

This type of mount is fine for gas engines but not for heavy diesels. This mount, on a brand new 45 footer, is badly distorted. Note how it is cocked toward the engine and forward. In this case, the mounts allowed the engine to move so much that the shaft coupling came apart.
However, the primary reason why drive systems do not stay in line indefinitely is due to wear and tear on all the components that make up the system. Stress, vibration, friction, slamming and pounding are all factors that contribute the the changing size and shape of all physical objects. Foremost among these are the engine mounts. Remember that it is the engine mounts that carry nearly all of the thrust load of the propeller and transfers it to the hull. Obviously, then, the engine mounts should be well-designed and strong. Unfortunately, more often than not the builder has selected the most inexpensive mounts that he can buy, mounts that are not going to do a very good job of keeping the system in alignment.
In fact, the most commonly used engine mounts for gas and small diesels is a mount that does a very poor job of maintaining alignment. Shown in the photo above, this mount not only permits the engine to rock forward and back, but up and down and laterally also. It literally allows the engine to move like a hobby horse.
A basic rule in engine alignment system is that that larger the vessel, the longer and larger diameter the shaft, the more critical alignment is. That's because any misalignment becomes magnified over the length of the shaft; the longer the shaft, the greater the potential error. A shaft that's centered at the strut bearing can easily be off by several inches with only a change in a degree or two of angle at the engine. This factor is what accounts for why shaft misalignment can cause so much damage on any shafting system of considerable length.
This is also why small boats can get away with a great deal of misaligment, and why they can get away with using cheap, inferiror mounts. A shaft that is only ten feet long can tolerate ten times the amount of misalignment of a shaft that is twenty feet long. But by the time you get up to a fourty-footer with a 15' shaft, the amount of movement and misalignment in the system that it can tolerate without causing damage declines dramatically.
At this point, the thickness and mass of both the shaft, propellor and the drive load all begins to play an increasingly important role. The reason is simply because small diameter shafts are much more elastic than large diameter shafts. All boat shafting systems are self-centering to some degree, but the larger the diameter shaft, the less self-centering it becomes. The shaft does not bend but transfers all that misdirected energy (vibration) to other components such as struts, bearings, transmission and the engine mounts.
The first thing to do is to check the engine mounts. If they are the vertical stud type set in a rubber base, these are the kind that are prone to rocking back and fourth. Check the stud to make sure that its centered in the base with the vessel at rest. If its leaning in any direction, the mount is stressed and the system is out of alignment (see photo #2).
Conduct a back down test. One engine at a time, start from neutral, put the engine in gear and accelerate hard, up to no more than 1/3 throttle. Repeat this process in reverse, all the while watching the mounts for movement. If the engine and mount are moving more than 1/8" in any direction, your mounts are not doing their job of holding the engine in place.
Observe the shafts while running at two speeds, idle and cruise. Observation of shaft runout will only prove the negative; out of line shafts can appear to run true even though out of line. On the other hand, a badly wobbling shaft means something's wrong. Runout up 1/8" is acceptable at idle speeds but not at cruise. If shaft wobble is visible over 1200 RPM, suspect a problem. Again, that's becasue rotating shafts tend toward self-centering. At high speed enven bent shafts can straighten out and show no sign of trouble. If the shaft is observably causing the transmission to move, or you can feel the movement by putting your hand on it, then there's definitely a problem.
Many boat yards think that the way to check shaft alignment is to disconnect the coupling and check the flange clearance with a feeler gauge. That's only part of the story. Before doing this, with the vessel hauled, check the position of the shafts relative to the bearings. Cutless bearings that are worn more on one side than another are a positive indicator that something is out of alignment. Heavy shafts of 1.5" or more will naturally compress the rubber bearing on the bottom side, but not so much that there's an obvious gap at the top. Photo #1 illustrates a clearly misaligned shaft.
Next, check the shaft-to-bearing alignment at both the front and back ends of the bearing. If the shaft is off-centered, either to one side, top or bottom at one end, but is off-centered to the opposite side at the other end, then the shaft is not parallel with the bearing bore. It is either up or down, or off to one side. In this case, the whole system should be suspect, at which point the entire system alignment must be redone, including setting up target wire to make sure that the struts themselves are properly aligned.
Now check how the shaft is centered with the opening in the stuffing box flange. If there is little clearance (shaft in the opening), it should be exactly centered; if a lot of clearance, it can be off a little without causing harm.
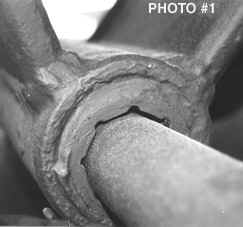
Judging by the large gap at the top, this bearing looks like it is worn. Actually it is new but the shaft is badly misaligned with the strut. This is determined because the gaps are on the opposite side of the bearing at the front side of the strut. Thus, the shaft is "cocked" in the bearing.
When there is significant misalignment involved, the struts and strut bolts should be checked. To do this, I usually pick a heavy piece of shoring found in most boat yards and give the strut several good whacks. If the strut deflects or shudders, its not stable. If water squirts out from the base, its loose. Also note whether the whole bottom of the hull is defecting when you hit the strut. If so, there's no point in realigning anything unless you first do something to make the strut base stable. If the struts are fluttering because the bottom is weak, the entire system is unstable and must be corrected.
Recently a number of articles have appeared in boating publications about dial indicating shafts while in the boat. I'll explain why this should never be done. As noted above, boat hulls can and do change shape over time. Further, the shape of the hull changes when hauled versus afloat. The changing shape of the hull is likely to cause the shaft to bend. Now, you may look at a 1.5" stainless shaft and think that it's cannot be easily bent. In fact, if you suspend it on its ends, even gravity will bend it considerably. Gravity will bend a 15' shaft a lot.
Finally, when you rotate the shaft by pulling on the propeller, you're moving the shaft against the rubber bearing, further throwing your dial indicator readings off. As any trained machinist will tell you, there's only one way to dial a shaft and that is on a calibrated roller bed. One simply cannot dial a rotating object without a reference base and expect accurate results. And a shaft in a boat doesn't provide such a reference.
Only after all the above checks have been made and proven that all else is in order, should one then procede to use the feeler gauges on the coupling. The problem with using feeler gauges is that this measurement can give a false indication that all is well. Particularly smaller shafts can be out of alignment at one end and yet still give a favorable reading at the coupling end. This is because shafts with multiple bearings can bend it into a favorable position while overall it is still badly out of alignment.
This is a very common problem on small to midsize boats. If you want to understand just how important strong struts are, just take a look at the huge struts used on larger Bertrams, Hatteras or Viking yachts. They don't spend all that money on massive struts for no reason. When there are hundreds of thousands of dollars at stake in machinery, the drive support system must be strong.
A futher fact to consider is that the smaller and less the value of the boat is, the less the amount real engineering has gone into its design. The drive system is one area that is often shortchanged.
Take a close look at the strut arm length to strut base ratio. Or, in otherwords, the ratio of the base footprint to the strut length. Also look at the strut width and cross-sectional thickness. In photograph #3, notice how long the strut arm is and how narrow the width is. The arm to width ratio is over 3:1 while the length to base ratio is more that 2:1. The extreme amount of leverage that the arm applies to the base means that it can't possibly hold the shaft steady. It will deflect and allow the shaft and propeller to oscillate.
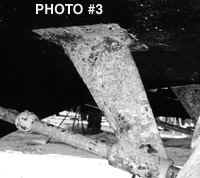
The strut in photo #3 carries the same size shaft and prop as in #2, both on a 40' boat. But the later is double the thickness in both width and cross-sectional area, with a substantiallly wider base. There is no doubt that this strut will hold the shaft steady. Also notice that the length of the strut bore is double the length of that in photo #2.
This strut will hold the shaft very steady, and because of this, correct engine/shaft alignment is much more critical. If its not correctly aligned, something will have to give, and whatever that is is likely to be expensive. The same holds true for shafts with double struts. In fact, a double set of struts will hold a shaft in even closer tolerance. As a general rule, shafts under 1.5" tend to be self-centering because they will bend so some small degree. But shafts larger than this do not take well to bending. They will not bend but work to tear the system apart if not correctly aligned.
Another general rule is that the larger the shaft diameter and the more bearings it has, the more critical are the engine mounts. Unless the mounts are holding in the engine in place and not permitting any movement, there's no point in trying to achieve proper alignment of anything. If the engine moves, no other part of the system will stay in alignment either.
Still another source of engine mount, strut bearing, vibration and shafting problems results from engines that are mounted on weak stringers, or on a hull bottom that is flexing. There are literally thousands of boats that have this problem. During the course of sea trials I frequently encounter engines that are shuddering and bouncing around to such a degree that the entire drive system is being damaged, from engine mounts all the way back to the strut bearings.
Engines mounted on weak stringers frequently results in transmission failures. This is because the worse part of the misalignment is being absorbed by the transmission coupling and output shaft bearings. The problem is usually blamed on the transmission when the source of the problem is really the hull itself. For boats that have had a history of transmission failures, this is something that should be checked first, before blaming the machinery or faulty repairs.
Only after checking all of the above points and making sure that all is in order should the transmission to shaft coupling alignment be checked.
Posted in 1997

David Pascoe - Biography
David Pascoe is a second generation marine surveyor in his family who began his surveying career at age 16 as an apprentice in 1965 as the era of wooden boats was drawing to a close.
Certified by the National Association of Marine Surveyors in 1972, he has conducted over 5,000 pre purchase surveys in addition to having conducted hundreds of boating accident investigations, including fires, sinkings, hull failures and machinery failure analysis.
Over forty years of knowledge and experience are brought to bear in following books. David Pascoe is the author of:
- " Mid Size Power Boats " (2003)
- " Buyers’ Guide to Outboard Boats " (2002)
- " Surveying Fiberglass Power Boats " (2001, 2nd Edition - 2005)
- " Marine Investigations " (2004).
In addition to readers in the United States, boaters and boat industry professionals worldwide from nearly 80 countries have purchased David Pascoe's books, since introduction of his first book in 2001.
In 2012, David Pascoe has retired from marine surveying business at age 65.
On November 23rd, 2018, David Pascoe has passed away at age 71.
Biography - Long version
Marine Engines Articles At A Glance
- More on Performance Diesels
- Comparing Diesel Types
- Diesel Engines
- Power Options
- Gas -vs- Diesel - Part II
- Gas Engines
- Drive System Alignment
- Problems with Engine and Shaft Alignment
- Exhaust Risers
- From Other categories
- "It's Got Recent Overhauls!" from Buying a Boat
- "What Does an Overhaul Entail?" from Buying a Boat

- Basic Considerations
- Boat Types: Which is Right for You?
- Old Boats, New Boats and Quality
- Basic Hull Construction
- Evaluating Boat Hulls
- Performance and Sea Keeping
- Decks & Superstructure
- Stress Cracks,Finishes and Surface Defects
- The Engine Room
- Electrical & Plumbing Systems
- Design Details
- Steering, Controls, Systems & Equipment
- The Art of the Deal
- Boat Shopping
- The Survey & Post Survey
- Boat Builders by Company

- What is Pre-Purchase Survey?
- Business Practices and Client Relations
- Sound vs. Seaworthiness
- Hull and Its Structure
- Surveying the Hull
- Using Moisture Meters
- Stress Cracks & Surface Irregularities
- Deck & Superstructure
- Drive Train
- Fuel Systems
- Exhaust Systems
- Electrical Systems
- Plumbing Systems
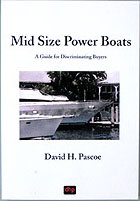
Published by: D. H. Pascoe & Co., Inc. Articles, Images: Copyright © 1997 - 2018 David H. Pascoe All rights reserved. Articles, Images: Copyright © 2019-2022 Junko A. Pascoe All rights reserved. Web site design & developement: Copyright © 1997 - 2023 Junko A. Pascoe All rights reserved. Web site: Maintained by Junko A. Pascoe

- Forums New posts Unanswered threads Register Top Posts Email
- What's new New posts New Posts (legacy) Latest activity New media
- Media New media New comments
- Boat Info Downloads Weekly Quiz Topic FAQ 10000boatnames.com
- Classifieds Sell Your Boat Used Gear for Sale
- Parts General Marine Parts Hunter Beneteau Catalina MacGregor Oday
- Help Terms of Use Monday Mail Subscribe Monday Mail Unsubscribe
Prop Shaft Alignment
- Thread starter Quality Time
- Start date Nov 23, 2004
- Hunter Owner Forums
- Mid-Size Boats
Quality Time
I just bought a 1992 H28. It has a significant vibration in the prop shaft at any RPM. While motoring I felt the vibration thoughout the entire hull and went below and looked at the stuffing box assembly and noticed that an oval was being worn in the plastic stuffing box. As a winter project, I plan to align the engine and shaft. At the same time, I'd like to replace all the parts (e.g., stuffing box, hose around shaft, etc.) where the shaft goes through the hull.Does anyone have advice on where to get the parts and how to do the alighnment? I read the Yanmar manual and it looks easy enough, in theroy, but what's the real deal? Does anyone have an opinion on plastic stuffing boxes (as compared to bronze)? Thanks for any input.
Pat McCartin
Alignment Replacing the parts over winter is a good project. You might also consider replacing the cutlas bearing. I'd take the shaft to a machine shop and have the "trueness" checked.**DO NOT ALIGN THE BOAT ON STANDS**The boat MUST be aligned in the water in its natural state. Do all the repairs over winter. In the spring splash her and let her sit for a few days then align the engine. Patientce is a virtue when doing alignments.Pat McCartinInland Marine DieselBuford, Ga[email protected]

Fred Ficarra
Wow, Pat, complex subject boiled down do its' essence. Good job.
Fred, Thanks for the compliment!
Alignment While replacing "parts", don't forget the engine mounts, a most important item.
A dripless seal might be a good idea Mine works well and I have a dry bilge. The down side is that if the rubber bellows gets torn, punctured, etc. it is a serious hazard for leaking.I think it is called a PSS from PYI inc. http://www.pyiinc.com/They have other products to consider as well like drive line parts, bearings, etc.They have treated me well in the past.I am not sure why you would need to replace engine mounts as a general maintainance item.Take a hard look at the prop while you are at it. We went from a two blade to a three blade and it made a huge difference all around - vibration was much less and we got a lot more power and speed.
Stuffing Box Unless they get frozen together bronze stuffing boxes last 50 years or longer. Replace the packing material with teflon flax available at marine discount suppliers for under ten bucks. The hose isn't due yet but change it if it will make you feel better.Avoid the overpriced over rated dripless systems. Besides being expensive they are a pain in the butt and you'll likely have to replace it long before your stuffing box
Daryl, what is painful about a dripless seal other than the price? I have had one for 8 years and no problem at all except that I have to vacuum the dust out of my bilge.I do worry about its safety and am very careful with it but I worry about the guy anchored next to me too.
Patrick, dripless response Several of my yacht club friends like to spend money on their vessels. Two of the four I know that used these things had complications, leaks, and parts replacement. They are a pain to install. Boat has to be hauled, coupling has to come off the shaft, (one of the four had to cut the shaft to get it apart). The concept is great but a properly maintained bronze stuffing box will last over 50 years and cost a small fraction of the dripless system. Being a Hunter owner with modest income (cheap) it seems like a bad investment that will require expensive maintenance in the future. The ten bucks I spent on teflon flax will last for the lifetime of my boat.
Well, Daryl I guess I would not have bought one of these either but it was already on the boat. So I have no bad experience to relate to your friends. It has been no problem at all in the time I have had it. No leaks and no wear that I can see. A dry bilge is pretty nice. If you have the funds, it is a nice mod to have.

Daryl, right on. I'll stick with my bronze... stuffing box, too. Terry
Terry, I'm with Daryl on this one too. I installed one of those bellows jobbies back when they first came out. It nearly sank the boat TWICE. But I'm sure they are better now!? I removed it at the next haul out. When I learned of Drip-Free packing, I installed it. (1988 or so) No haulout needed, cost $35.00 and it's still working today. Dry bilge and a loose shaft. A perfect product.
Engine Mount Replacement?! If the mounts look good (no cracks, dry rot, etc.) would you still replace them anyway. Another way to ask this question is: how do you know that your engine mounts need to be replaced?
- This site uses cookies to help personalise content, tailor your experience and to keep you logged in if you register. By continuing to use this site, you are consenting to our use of cookies. Accept Learn more…

VIDEO
COMMENTS
You must first take the wobble out of it, then align the coupling flange on the transmission to the flange on the forward end of the shaft. Here's one series of tricks that actually works if your boat is out of the water. 1. Loosen the hose clamps and remove the rubber boot from the front end of the shaft log. 2.
Prop shaft alignment. Nearly all marine engines are designed to be adjustable, to a point, relative to the propeller shaft by using adjustment or jacking nuts on their motor mounts. The adjustment should be thought of as no more than fine-tuning, the maximum range of vertical travel being limited to no more than an inch or two at the most ...
The alignment you will be checking is the space between the propeller shaft coupler and the output coupler from either the transmission or the v-drive. 1) Locate and identify the propeller shaft coupler. On inboards, it's easy to see at the end of the transmission and on a wakeboat, has 4 bolts connecting it to the propeller shaft coupler.
As the shaft bearings are aligned, the engine is also brought into precise alignment with the shaft. "Even experienced yacht people think that if you get the two faces of the propeller shaft coupling exactly parallel, the engine is aligned, but you've got a huge amount of weight, seven or eight feet of shaft and a heavy coupling, hanging out there unsupported once it leaves that last ...
162. Catalina 36MKII Waukegan, IL. May 29, 2014. #1. Over the winter I pulled the transmission and installed a new damper plate. While at it I replaced the bellows on the PYI dripless shaft seal. This spring I notice I have wobble in the prop shaft. So I checked alignment and it is out more than the recommended .003 at the coupling.
Engine and propeller shaft alignment are among the most critical aspects of propulsion system installation, reliability and maintenance. Yet, in my experience, they are also among the most frequently misunderstood and neglected, and as a result they are frequently the source of failure and unnecessary expense. ... Palm Beach International Boat ...
THE OTHER ALIGNMENT. There is another side to the alignment story; it involves the support and position of the propeller shaft relative to its bearing(s), the shaft log and the engine. While engine alignment is well understood by most marine industry professionals, shaft alignment is far more esoteric and well understood by far fewer folks in the industry.
376 posts · Joined 2006. #10 · Feb 23, 2007 (Edited) There are three steps to shaft alignment. 1. Center the shaft in the stern tube. Usually done with the coupling disconnected. The goal is to place the centerline of the shaft as close to the centerline of the stern tube/stern gland as possible.
WOULD LIKE TO GET ON BOARD BRUPEG?If you want to see all of Brupeg's episodes and behind the scenes bonus content, help make the channel & boat great plus ph...
Now that I've recon the engine mounts and after watching a Youtube instructional video on engine/shaft alignment, I when ahead an get the alignment done. But somehow I still has this feeling that the alignment is not quite right. Vibrate seems alittle more than before I started this recon work...
Nov 6, 2006. 9,846. Hunter 34 Mandeville Louisiana. Oct 6, 2014. #4. The check to complete before launch is to make sure that when the shaft is centered in the log, it is not binding in the Cutless. once in the water, you can do the engine alignment to the shaft while the shaft is blocked to the center of the log.
Measure the gap at the top and the bottom. Subtract one from the other. Turn the shaft 90 degrees, perform this again. The difference values you calculate should be the same if it's perfectly straight. Don states helpfully that if the "gap changes dramatically", then there is a problem.
The maximum tolerance for shaft wear is just one thousandth of an inch. The shaft shown here has been condemned as a result of excessive wear, caused by gross misalignment. In last month's column I reviewed the importance of, and techniques for, ensuring proper engine alignment. That is, the alignment between the engine and the propeller shaft.
General Boat Parts. Split Hub Shaft Couplings; Groco Raw Water Strainers; ... Split Hub Propeller Shaft Coupling Kit (ZF 800 80 85 A/IV, ZF 220PL, 280A/IV, 286A/IV, 301, MG506 5061 507) ... Home » Tony's Tips » Articles » All about Propeller Shaft Alignment.
With the boat out of the water, you can check the shaft alignment yourself by checking how the shaft aligns to the cutlass bearing. Needless to say, you can only do this with a bearing that is not worn. ... The strut in photo at bottom carries the same size shaft and prop, both on a 40' boat. But the later is double the thickness in both width ...
Re: Prop shaft alignment: on the hard or in water? Definitely better in water where boat/engine operate. Should actually be floating for 24 hours or longer before aligning, so Boat can take it's floating shape based on keel hanging rather than boat sitting on it and impact of rigging load.
CDK retired engineer. The shaft alignment is simple and can be done without special equipment. Once the shaft is removed and new cutlass bearings in place you could use a laser to check the alignment, but when you push the shaft back in, you certainly feel if one of the bearings is off center. The engine is a different matter, because even with ...
Apr 14, 2009. #1. Working on rebuilding a true inboard. I have read the prop shaft alignment guide from Borg Warner and they are very specific and the tolerances are .003 of parallel between the output shaft and the prop shaft couplers. To align, the engine has to be moved at all 4 corners. The motor mounts allow up and down adjustment via a ...
We recently purchased a 1990 Hunter 30 while she sat in the water and when we got her on the hard, we noticed the shaft strut was bent to the starboard, I plan on removing the strut and gettng it to a local machine shop for repairs and in the meantime I'm planning the re-install and can't see...
Applying a calculated lift can offset shaft sag while aligning running gear. For example, 4′ (1.2m) of 2″ (51mm) shaft weighs 42 lbs (19 kg), divided by 2 is 21 lbs (9.5 kg), plus the weight of the coupling—which we'll say is 22 lbs (10 kg)—equals 43 lbs (19.5 kg). Lifting 43 lbs at the coupling end of the shaft will negate the effect ...
In 2012, David Pascoe has retired from marine surveying business at age 65. On November 23rd, 2018, David Pascoe has passed away at age 71. When it comes to yacht maintenance, one of the least understood and most overlooked systems that require maintenance, engine and shaft alignment probably heads the list.
I just bought a 1992 H28. It has a significant vibration in the prop shaft at any RPM. While motoring I felt the vibration thoughout the entire hull and went below and looked at the stuffing box assembly and noticed that an oval was being worn in the plastic stuffing box. As a winter project...